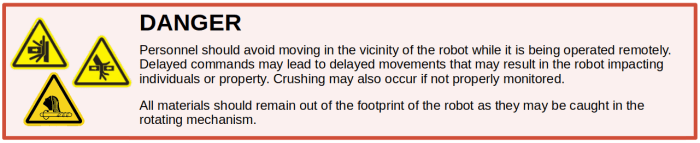
The safety spectrum of teleoperation is a fascinating area of robotics that explores the delicate balance between human control and machine autonomy. Imagine controlling a robot arm thousands of miles away, performing complex tasks in hazardous environments. This is the world of teleoperation, where humans extend their capabilities through technology, but safety is paramount.
We’ll delve into the factors influencing teleoperation safety, from human-machine interaction to communication latency, and explore the different levels of autonomy that shape this field.
Teleoperation systems are used in various industries, from healthcare and manufacturing to space exploration and disaster response. Each application presents unique challenges, demanding innovative solutions to ensure safe and reliable operation. Understanding the safety spectrum of teleoperation is crucial for developing future systems that are not only efficient but also secure and reliable.
Introduction to Teleoperation: The Safety Spectrum Of Teleoperation
Teleoperation refers to the control of a remote device, often in a hazardous or inaccessible environment, by a human operator using a control interface. It involves the extension of human capabilities to distant or dangerous locations, enabling tasks that would be impossible or unsafe for humans to perform directly.
The concept of a “safety spectrum” in teleoperation acknowledges the varying levels of autonomy and human involvement in different systems. This spectrum ranges from fully manual teleoperation, where the operator has complete control over the remote device, to fully autonomous systems, where the device operates independently without human intervention.
Key Components of Teleoperation
Teleoperation systems typically consist of several key components:
- Operator Interface:This provides the human operator with the necessary controls and feedback to manipulate the remote device. The interface can include joysticks, haptic devices, and visual displays, allowing the operator to control the device’s movements, receive sensory information, and monitor its status.
- Communication Channel:This transmits control signals from the operator to the remote device and feedback information back to the operator. The communication channel can be wired, wireless, or a combination of both, and its reliability and latency are crucial for effective teleoperation.
- Remote Device:This is the actual device that is controlled by the operator. The remote device can be a robot, a vehicle, a surgical tool, or any other equipment that needs to be operated remotely. Its design and capabilities depend on the specific application.
The safety spectrum of teleoperation is a complex topic, ranging from completely autonomous systems to fully manual control. Finding the right balance depends on the task at hand, and, like the saying birds of a feather flock together , it often means bringing together experts with complementary skills.
By collaborating with engineers, operators, and safety specialists, we can develop systems that are both effective and safe.
- Control System:This interprets the operator’s commands, processes sensory feedback, and generates control signals for the remote device. The control system can be based on various algorithms and technologies, including classical control, artificial intelligence, and machine learning.
Examples of Teleoperation Systems
Teleoperation systems have found applications across various industries, including:
- Robotics:Remotely controlled robots are used in hazardous environments such as nuclear power plants, disaster zones, and underwater exploration. These robots can perform tasks such as inspection, maintenance, and manipulation of objects.
- Surgery:Teleoperated surgical instruments allow surgeons to perform minimally invasive procedures with greater precision and control. Robotic surgery systems enable surgeons to operate on patients from remote locations, offering advantages such as reduced recovery time and less scarring.
- Aerospace:Teleoperated spacecraft and drones are used for tasks such as space exploration, planetary landing, and reconnaissance. These systems enable humans to explore and interact with the environment remotely, overcoming the limitations of traditional space exploration methods.
- Mining and Construction:Teleoperated heavy machinery is used in dangerous and demanding environments, such as underground mines and construction sites. These systems allow operators to control equipment remotely, reducing risks and improving efficiency.
Factors Influencing Teleoperation Safety
Teleoperation safety is a multifaceted issue that requires a comprehensive understanding of the factors influencing the performance and reliability of teleoperation systems. The safety of the operator, the environment, and the remote asset are all paramount considerations.
The safety spectrum of teleoperation is a fascinating area, balancing the potential for incredible progress with the need for robust safeguards. It’s a bit like building a delicious cheese board – you need a variety of components, each playing a crucial role.
And just as you might want to try a new approach to arranging your fruit slices, diy a fruit slice cheese board , so too do we need to be creative in how we design safety systems for teleoperated robots.
Ultimately, both require careful planning and attention to detail to ensure a satisfying outcome.
Human-Machine Interface (HMI)
The HMI serves as the bridge between the operator and the remote system. It plays a crucial role in operator performance and safety by providing a clear and intuitive means of control and information feedback. An effective HMI design is essential for minimizing operator workload, enhancing situational awareness, and facilitating rapid response to unexpected events.
- Intuitive and user-friendly interface design:A well-designed HMI should be easy to understand and use, minimizing operator cognitive load and reducing the potential for errors. For example, using clear and concise icons, intuitive controls, and a logical layout can significantly enhance operator performance.
- Real-time feedback and data visualization:Providing operators with real-time information about the remote environment and system status is critical for informed decision-making. This includes visual representations of sensor data, system parameters, and operational status. For example, displaying the remote robot’s position, orientation, and sensor readings in a clear and easily interpretable format can help operators maintain situational awareness and anticipate potential hazards.
Thinking about the safety spectrum of teleoperation, it’s a fascinating mix of technical challenges and human factors. You’ve got to consider everything from latency and network reliability to operator fatigue and situational awareness. It’s almost like a high-stakes game of chess, where every move has consequences.
It’s also interesting to see how this field is influencing other industries, like fashion, where the work of visionary stylist Sam McKnight, who recently received the Isabella Blow Award, a testament to his creative impact , is shaping the way we see beauty.
Ultimately, both teleoperation and fashion design are about pushing boundaries and finding innovative solutions, which is why they both demand a deep understanding of risk and safety.
- Haptic feedback and force reflection:Incorporating haptic feedback into the HMI can enhance operator perception and control by providing tactile information about the remote environment. Force reflection, in particular, allows operators to feel the forces and resistances encountered by the remote robot, providing a more intuitive and realistic sense of interaction.
For example, in surgical teleoperation, haptic feedback can provide surgeons with a more precise sense of tissue stiffness and manipulation forces, improving surgical accuracy and minimizing tissue damage.
Communication Latency and Bandwidth
Communication latency, the time delay between sending a command and receiving feedback, is a critical factor in teleoperation safety. High latency can lead to delays in operator response, hindering their ability to react to dynamic situations and potentially causing accidents.
Similarly, insufficient bandwidth can limit the amount of data transmitted between the operator and the remote system, affecting the quality of feedback and hindering real-time control.
- Impact of latency on operator performance:High latency can significantly impact operator performance by delaying their responses and reducing their ability to control the remote system accurately. For example, in teleoperated vehicle navigation, high latency can lead to jerky movements and difficulty in maneuvering the vehicle through tight spaces.
- Minimizing latency and bandwidth constraints:Strategies for minimizing latency and bandwidth constraints include using high-speed communication networks, employing data compression techniques, and optimizing data transmission protocols. For example, using fiber optic cables or dedicated satellite links can significantly reduce communication latency, while data compression algorithms can reduce the amount of data transmitted without compromising essential information.
Redundancy and Fault Tolerance
Redundancy and fault tolerance are crucial aspects of teleoperation system design, ensuring continued operation in the event of component failures. Implementing redundant systems and components allows for continued operation even if one or more components fail, while fault tolerance mechanisms enable the system to adapt to unexpected events and maintain safe operation.
- Redundant systems and components:Redundancy can be achieved by using multiple actuators, sensors, or control systems. For example, in a teleoperated robot, having two independent control systems can ensure continued operation even if one system fails.
- Fault detection and recovery mechanisms:Fault tolerance involves implementing mechanisms to detect and recover from failures. This can include monitoring system parameters, identifying potential malfunctions, and automatically switching to backup systems or reconfiguring the system to maintain operation. For example, a teleoperated vehicle may be equipped with sensors to detect wheel slippage or engine malfunctions, allowing the system to automatically adjust control parameters or activate emergency braking systems.
Environmental Factors
Environmental factors can significantly influence teleoperation safety, posing potential risks to the operator, the remote environment, and the remote asset. Understanding and mitigating these risks is essential for safe teleoperation.
- Environmental hazards and conditions:Teleoperation tasks often involve hazardous environments, such as underwater, underground, or in areas with extreme temperatures or radiation. Understanding the specific hazards of the environment and implementing appropriate safety measures is crucial. For example, teleoperated robots operating in underwater environments may need to be equipped with sensors to detect and avoid underwater obstacles, while those operating in hazardous environments may need to be equipped with protective shielding or remote monitoring systems.
- Environmental sensing and monitoring:Providing operators with real-time information about the remote environment is essential for safe operation. This includes data from sensors such as cameras, microphones, and environmental sensors. For example, in a teleoperated mining operation, operators may need to monitor the concentration of harmful gases or the stability of the mine walls using remote sensors.
Levels of Autonomy in Teleoperation
Teleoperation systems span a spectrum of autonomy, ranging from complete human control to fully autonomous operation. This spectrum reflects the increasing reliance on automation and artificial intelligence in teleoperation. Understanding the different levels of autonomy is crucial for comprehending the safety implications and potential applications of these systems.
Levels of Autonomy in Teleoperation
The level of autonomy in a teleoperation system refers to the degree of control that the human operator has over the remote system. The autonomy levels are typically categorized as follows:
- Telepresence: This level represents the most direct human control, where the operator directly manipulates the remote system through a physical interface. This level provides the highest level of human oversight and control but can be physically demanding and require significant operator skill.
- Shared Control: In this level, the operator shares control with the autonomous system. The system can assist the operator with tasks like path planning, obstacle avoidance, or stabilization, but the operator retains ultimate control. This level aims to reduce operator workload and enhance performance while still providing human oversight.
- Supervisory Control: In this level, the operator oversees the operation of the autonomous system. The system can execute tasks autonomously based on pre-programmed instructions or learned behavior, but the operator can intervene and take control if needed. This level allows for increased efficiency and reduces the need for constant human input, but it requires a robust system for monitoring and intervention.
- Autonomous Control: This level represents the highest level of autonomy, where the system operates completely independently of human intervention. The system can plan, execute, and monitor tasks without any human input. This level offers significant potential for efficiency and performance but raises significant safety concerns due to the lack of human oversight.
Safety Implications of Autonomy Levels
The safety implications of teleoperation systems vary depending on the level of autonomy.
- Telepresence: In telepresence systems, the operator directly controls the remote system, providing the highest level of human oversight and control. This reduces the risk of unintended actions by the system but can lead to operator fatigue and errors due to the demanding nature of direct control.
- Shared Control: Shared control systems aim to improve performance and reduce operator workload but introduce the risk of system malfunction or unexpected behavior that could lead to accidents. The system’s decision-making algorithms and safety mechanisms must be robust to ensure reliable and safe operation.
- Supervisory Control: Supervisory control systems offer efficiency and reduced human workload but require robust monitoring and intervention capabilities. The system’s autonomy should be carefully designed to minimize the risk of unintended actions and allow for timely human intervention in case of unexpected events.
- Autonomous Control: Fully autonomous systems pose the greatest safety challenges due to the lack of human oversight. These systems require advanced safety features, including robust error detection and recovery mechanisms, to ensure reliable and safe operation. Extensive testing and validation are crucial to ensure the system’s safety and reliability.
Real-World Applications of Autonomy Levels, The safety spectrum of teleoperation
Different levels of autonomy find application in various real-world scenarios.
- Telepresence: This level is commonly used in surgical procedures, where the surgeon remotely controls robotic instruments to perform delicate operations. It is also used in remote inspection and maintenance tasks in hazardous environments.
- Shared Control: Shared control systems are employed in autonomous vehicles, where the driver shares control with the vehicle’s automated systems for tasks like lane keeping, adaptive cruise control, and parking. This level also finds applications in robotic assistants for manufacturing and logistics.
- Supervisory Control: Supervisory control systems are used in industrial automation, where robots perform repetitive tasks under human supervision. This level is also applied in drone delivery systems, where the operator oversees the drone’s flight path and monitors its progress.
- Autonomous Control: Autonomous control systems are being developed for applications like self-driving cars, where the vehicle operates completely independently of human intervention. This level also holds potential for applications in disaster response, space exploration, and other challenging environments.
Safety Measures and Protocols
Ensuring the safety of both the operator and the environment is paramount in teleoperation systems. Various safety measures and protocols are implemented to mitigate risks and prevent accidents. These measures address potential hazards associated with remote control, communication delays, and the inherent complexity of operating systems across vast distances.
Safety Standards and Regulations
Safety standards and regulations play a crucial role in guiding the design, implementation, and operation of teleoperation systems. These standards provide a framework for establishing acceptable safety levels and ensuring compliance with best practices.
- ISO 13482:2014:This standard specifically addresses the safety of medical devices used in teleoperation, focusing on the design and testing of teleoperated surgical systems.
- IEC 61508:This international standard Artikels the functional safety of electrical/electronic/programmable electronic systems, providing a framework for assessing and managing risks associated with teleoperation systems.
- ANSI/RIA R15.06-2012:This standard focuses on the safety of industrial robots, including teleoperated robots, providing guidelines for design, operation, and maintenance.
These standards ensure that teleoperation systems are developed and deployed with safety as a primary consideration, fostering a safer environment for operators and the surrounding environment.
Emergency Stops and Fail-Safe Modes
Teleoperation systems incorporate emergency stop mechanisms and fail-safe modes to handle unexpected situations and minimize potential risks. These features are essential for responding to system malfunctions, operator errors, or unforeseen events.
- Emergency Stop Buttons:These buttons are strategically placed on the operator interface, allowing for immediate halting of the teleoperated system in case of an emergency.
- Fail-Safe Modes:These modes are designed to bring the system to a safe state in case of communication failure or system malfunction. This can involve stopping the system, moving it to a designated safe position, or reducing its operating speed.
These measures provide an immediate and effective response to critical situations, minimizing the potential for harm to the operator, the environment, or the teleoperated system itself.
Remote Monitoring and Supervision
Remote monitoring systems provide real-time visibility into the teleoperation system’s operation, enabling operators and supervisors to monitor critical parameters and identify potential hazards.
- System Health Monitoring:This involves tracking key system parameters like power levels, sensor readings, and communication status, alerting operators to potential issues or malfunctions.
- Operator Performance Monitoring:This involves tracking operator actions and performance, allowing supervisors to identify potential errors or fatigue and provide guidance or intervention when necessary.
- Environmental Monitoring:This involves monitoring the surrounding environment of the teleoperated system, detecting hazards such as obstacles, personnel, or environmental conditions that may pose risks.
Remote monitoring systems enhance situational awareness and allow for timely intervention, significantly contributing to overall system safety.
Challenges and Future Directions
While teleoperation offers significant benefits, ensuring safety remains a paramount concern. Addressing the inherent challenges and exploring emerging technologies is crucial to unlocking the full potential of teleoperation systems.
Key Challenges in Teleoperation Safety
The inherent complexities of teleoperation systems present numerous challenges in ensuring safety. These challenges stem from factors such as latency, communication disruptions, human error, and the need for robust control mechanisms.
- Latency and Communication Disruptions:Delays in communication between the operator and the remote system can lead to misjudgments and accidents. Additionally, communication disruptions can result in loss of control or incomplete information transmission.
- Human Error:Operator fatigue, stress, and inexperience can contribute to errors in decision-making and control.
- Control System Complexity:Teleoperation systems involve intricate control mechanisms that require careful design and implementation to ensure stability and responsiveness.
- Environmental Uncertainty:Unpredictable environments can pose significant safety risks, as the operator may not have complete information about the surroundings.
Emerging Technologies for Enhanced Teleoperation Safety
Advancements in artificial intelligence (AI), robotics, and communication technologies are paving the way for more robust and safe teleoperation systems.
- AI-Powered Predictive Modeling:AI algorithms can analyze real-time data from the remote environment and predict potential hazards, enabling proactive safety measures.
- Haptic Feedback:Haptic feedback systems provide operators with a realistic sense of touch, enhancing situational awareness and control.
- Collaborative Teleoperation:This approach involves multiple operators working together to control the remote system, leveraging individual expertise and reducing the risk of human error.
- Autonomous Safety Features:Autonomous features, such as collision avoidance and emergency braking systems, can enhance safety by mitigating potential hazards.
Hypothetical Teleoperation System for Enhanced Safety
Imagine a teleoperation system designed to address current safety concerns and promote future advancements.
- AI-Assisted Control:The system incorporates AI algorithms to analyze real-time data from the remote environment, predict potential hazards, and provide recommendations to the operator.
- Advanced Haptic Feedback:The system provides operators with highly realistic haptic feedback, allowing them to experience the texture, shape, and force of objects in the remote environment.
- Redundant Control Mechanisms:The system employs multiple control mechanisms, including manual, semi-autonomous, and fully autonomous modes, ensuring a fail-safe approach.
- Integrated Safety Monitoring and Alerting System:The system constantly monitors the remote environment and operator performance, providing alerts in case of potential hazards or errors.