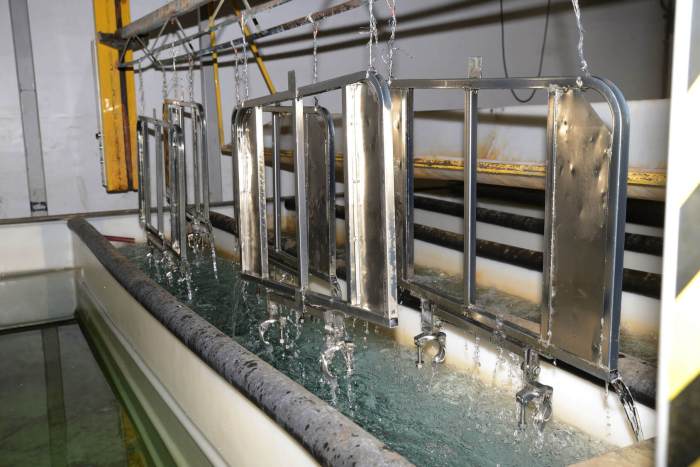
The howwhatwhy on metal plating – The How, What, Why of Metal Plating sets the stage for this enthralling narrative, offering readers a glimpse into a world where metal transforms, taking on new properties and applications. Metal plating, a process with roots in ancient history, has evolved into a sophisticated technology that plays a vital role in countless industries.
From the shimmering chrome on your car to the protective coating on your smartphone, metal plating is everywhere. It’s a process that involves depositing a thin layer of metal onto a substrate, altering its surface characteristics and enhancing its performance.
This blog delves into the fascinating world of metal plating, exploring the science behind it, the diverse types of processes available, and the wide-ranging applications that make it an indispensable technology.
The “How” of Metal Plating: The Howwhatwhy On Metal Plating
Metal plating is a fascinating process that involves depositing a thin layer of metal onto a substrate, transforming its properties and extending its lifespan. It’s a common technique used in various industries, from jewelry making to automotive manufacturing, and the “how” behind it is a combination of meticulous steps and precise control.
Surface Preparation
Surface preparation is crucial for successful metal plating. It ensures that the substrate is clean, free of contaminants, and ready to receive the plating. This step typically involves a series of treatments:
- Degreasing:This removes oils, greases, and other organic contaminants that can hinder adhesion. It’s often achieved using solvents, alkaline cleaners, or ultrasonic cleaning.
- Descaling:This removes oxides, scales, and other inorganic impurities that can interfere with the plating process. It’s often done using acids, such as hydrochloric acid, or mechanical methods like sandblasting.
- Etching:This creates a rough surface for better adhesion of the plating. It involves using acids to selectively remove material from the substrate.
- Rinsing:After each cleaning step, the substrate is thoroughly rinsed with water to remove any residual cleaning agents.
The quality of the surface preparation directly impacts the final plating quality. If the surface is not properly prepared, the plating may not adhere well, leading to defects and premature failure.
Plating Solution Preparation
The plating solution, also known as the electrolyte, contains the metal ions that will be deposited onto the substrate. The preparation of the plating solution is critical for achieving the desired plating thickness and properties.
The howwhatwhy on metal plating is fascinating, from the chemical reactions that create the protective layer to the diverse applications across industries. It reminds me of Elsie’s main bedroom tour, elsies main bedroom tour , where she explained the intricate details of her custom-made headboard, a piece of art that utilizes metal plating to achieve its unique finish.
It’s amazing how such a simple process can create such striking and durable results.
- Metal Salts:The plating solution contains the metal salts that provide the metal ions for deposition. The choice of metal salt depends on the desired plating metal and the desired properties of the coating.
- Additives:These are added to the plating solution to improve the plating process and the properties of the coating. Common additives include brighteners, levelers, and stress relievers.
- pH Control:The pH of the plating solution is carefully controlled to ensure optimal plating conditions. This is typically achieved by adding acids or bases.
- Temperature Control:The temperature of the plating solution is also carefully controlled to ensure the plating process occurs at the desired rate.
The plating solution is a critical component of the metal plating process, and its preparation must be precise to achieve the desired results.
Metal plating is a fascinating process, and I recently found myself thinking about the intricate details involved. It reminded me of a project I tackled recently – creating a gold cactus wallpaper DIY project. It’s amazing how the same principles of applying a thin layer of material for decorative or protective purposes apply to both metal plating and wallpaper projects.
I’m definitely inspired to explore more about the how, what, and why of metal plating!
Electroplating Process
The electroplating process is the heart of metal plating, where the actual deposition of the metal onto the substrate occurs. This process involves immersing the prepared substrate in the plating solution and applying an electric current.
- Electrolysis:The electric current causes metal ions from the plating solution to migrate towards the substrate, which acts as the cathode.
- Deposition:As the metal ions reach the cathode, they gain electrons and become neutral metal atoms, which then deposit onto the substrate.
- Current Density:The amount of current applied per unit area of the substrate is called the current density. This affects the plating rate and the properties of the coating.
- Plating Time:The duration of the plating process determines the thickness of the coating.
The electroplating process is a complex interplay of chemical and electrical factors, and careful control is essential for achieving the desired results.
Post-Plating Treatments
After the electroplating process, the plated substrate may undergo various post-plating treatments to enhance its properties and appearance. These treatments include:
- Rinsing:After electroplating, the substrate is rinsed with water to remove any residual plating solution.
- Drying:The substrate is then dried to prevent corrosion or other surface defects.
- Polishing:This improves the appearance of the plated surface and can enhance its corrosion resistance.
- Heat Treatment:This can improve the hardness, ductility, or other mechanical properties of the coating.
These post-plating treatments can significantly enhance the performance and longevity of the plated substrate.
The “howwhatwhy” of metal plating is fascinating! From protecting against corrosion to enhancing aesthetics, it’s a process with a lot of depth. It’s a bit like how Hawke Media recently acquired Lemonade Agency – hawke media acquires lemonade agency – both moves are about strengthening a core business and expanding reach.
Just like metal plating can transform a surface, this acquisition will likely reshape the marketing landscape, making it even more exciting to watch the evolution of the “howwhatwhy” of digital strategy.
Quality Control and Monitoring
Quality control is essential throughout the metal plating process to ensure consistent and reliable results. This involves monitoring various parameters and performing tests to ensure that the plating meets the required specifications.
- Plating Thickness:The thickness of the plating is a critical parameter that determines the performance and durability of the coating. It is typically measured using non-destructive methods such as eddy current testing or X-ray fluorescence.
- Adhesion:The adhesion of the plating to the substrate is essential for its longevity. It is typically tested using methods such as tape pull testing or scratch testing.
- Porosity:The presence of pores in the plating can compromise its corrosion resistance. It is typically tested using methods such as the salt spray test or the copper sulfate test.
- Appearance:The appearance of the plated surface is often important for aesthetic reasons. It is typically evaluated using visual inspection or microscopy.
Regular monitoring and quality control ensure that the metal plating process consistently produces high-quality coatings that meet the required specifications.
The “Why” of Metal Plating
Metal plating is not just a decorative process; it serves a critical role in enhancing the functionality and lifespan of various materials. Metal plating goes beyond aesthetics, offering a wide range of benefits that impact numerous industries.
Reasons for Metal Plating
The primary reasons for using metal plating are rooted in the desire to improve the properties of materials. Metal plating provides a protective barrier, enhances conductivity, and improves aesthetic appeal, among other advantages.
Examples of Enhanced Properties
Metal plating can significantly alter the properties of materials, making them more suitable for specific applications. Here are some examples:
- Corrosion Resistance:Plating materials like zinc, nickel, and chromium can form a protective barrier on the surface of metals, preventing corrosion and extending their lifespan. For instance, galvanized steel, coated with zinc, is commonly used in construction and automotive applications due to its superior resistance to rust.
- Wear Resistance:Hard chrome plating, known for its exceptional hardness, is widely used in tools, dies, and engine parts to improve wear resistance and extend their service life. The hard chrome layer reduces friction and abrasion, minimizing wear and tear during operation.
- Electrical Conductivity:Gold plating is frequently employed in electronic components and connectors due to its excellent electrical conductivity. This ensures efficient signal transmission and reduces signal loss, vital for high-performance electronic devices.
- Heat Resistance:Nickel plating is often used to enhance the heat resistance of components, particularly in high-temperature applications. It can withstand high temperatures without degrading, making it suitable for use in engines, furnaces, and other heat-intensive environments.
Applications of Metal Plating in Diverse Industries
Metal plating finds diverse applications across various industries, each leveraging its unique benefits to enhance product performance and longevity.
Automotive Industry
- Corrosion Protection:Zinc plating is widely used on car bodies and chassis to prevent rust and corrosion, extending their lifespan and maintaining their aesthetic appeal.
- Wear Resistance:Hard chrome plating is applied to engine parts like cylinder liners and piston rings to improve wear resistance, ensuring smooth operation and reducing friction.
- Decorative Finishes:Chrome plating is used for decorative purposes on car parts like bumpers, grilles, and wheels, enhancing their appearance and providing a durable finish.
Electronics Industry
- Conductivity Enhancement:Gold plating is used on electronic connectors, pins, and contacts to ensure efficient signal transmission and reduce signal loss. This is crucial for high-performance electronic devices, ensuring reliable data transfer and communication.
- Corrosion Protection:Nickel plating is used on electronic components to protect them from corrosion, particularly in humid environments. It helps maintain the integrity of the components and prevents electrical malfunctions.
- Surface Finish:Tin plating is often used on electronic components to provide a smooth and solderable surface, facilitating reliable connections and assembly processes.
Aerospace Industry
- Corrosion Resistance:Cadmium plating is used on aircraft parts to provide corrosion protection in harsh environments, such as high humidity and salt spray. This is crucial for maintaining the structural integrity of aircraft components.
- Heat Resistance:Nickel plating is used on aerospace components to enhance their heat resistance, allowing them to withstand high temperatures during flight. This is particularly important for components located near engines or in areas exposed to significant heat.
- Wear Resistance:Hard chrome plating is used on aircraft parts like landing gear and engine components to improve wear resistance, ensuring their reliability and longevity under demanding conditions.
Medical Industry
- Biocompatibility:Titanium plating is used on medical implants and devices to enhance their biocompatibility, minimizing the risk of rejection or infection. Titanium’s inert nature and ability to integrate with bone make it ideal for medical applications.
- Corrosion Resistance:Stainless steel plating is used on surgical instruments and medical devices to prevent corrosion and maintain their sterility. This ensures safe and effective use in sterile environments.
- Surface Finish:Gold plating is used on medical implants and devices to provide a smooth and biocompatible surface, reducing the risk of tissue irritation or rejection.
Other Industries
Metal plating has applications in numerous other industries, including:
- Tool and Die Manufacturing:Hard chrome plating is used to enhance the wear resistance and durability of tools and dies, extending their lifespan and improving their performance.
- Jewelry and Watchmaking:Gold, silver, and rhodium plating are used to enhance the appearance and durability of jewelry and watches, providing a luxurious finish and protecting them from tarnishing.
- Construction:Galvanized steel, coated with zinc, is widely used in construction for its corrosion resistance, making it suitable for roofing, fencing, and structural components.
Challenges and Considerations in Metal Plating
Metal plating, while a highly versatile and valuable process, is not without its challenges and considerations. Understanding these aspects is crucial for optimizing plating operations, ensuring product quality, and minimizing environmental impact.
Environmental and Safety Considerations
Metal plating processes often involve the use of hazardous chemicals, including heavy metals, acids, and alkalis. These substances can pose significant risks to human health and the environment if not handled properly. Here are some key considerations:
- Wastewater Treatment:Plating processes generate wastewater containing dissolved metals, chemicals, and other contaminants. Effective wastewater treatment is essential to prevent pollution of water bodies and protect public health. This typically involves processes like chemical precipitation, filtration, and ion exchange to remove pollutants.
- Air Pollution:Some plating processes release volatile organic compounds (VOCs) and particulate matter into the air. Proper ventilation systems and air pollution control technologies are needed to minimize emissions and protect worker health.
- Worker Safety:Workers involved in plating operations are exposed to various hazards, including chemical burns, respiratory problems, and skin irritations. Strict safety protocols, personal protective equipment (PPE), and regular health monitoring are essential to ensure worker safety.
Common Challenges in Metal Plating
Metal plating processes can face several challenges that can affect the quality and efficiency of the plating. These include:
- Adhesion:Poor adhesion of the plating to the substrate can lead to premature failure. Factors influencing adhesion include surface preparation, plating bath chemistry, and the nature of the substrate material.
- Porosity:Porosity in the plating can reduce its corrosion resistance and affect its appearance. Porosity can arise from improper plating conditions, insufficient current density, or the presence of impurities in the plating bath.
- Stress:Plating can induce stress in the substrate, potentially leading to cracking or warping. This is more likely to occur with thicker plating layers or when using materials with different thermal expansion coefficients.
- Uniformity:Achieving uniform plating thickness across the entire surface is crucial for consistent performance and appearance. Factors like the shape of the part, the distance from the anode, and the agitation of the plating bath can affect uniformity.
Future Trends and Advancements in Metal Plating, The howwhatwhy on metal plating
The field of metal plating is constantly evolving, driven by the need for more sustainable, efficient, and advanced plating processes. Here are some key trends and advancements:
- Electrochemical Deposition:Research focuses on developing novel electrochemical deposition techniques, such as pulse plating and reverse pulse plating, to improve plating efficiency, reduce energy consumption, and enhance the properties of the deposited metal.
- Nanotechnology:The use of nanotechnology in metal plating is gaining momentum. This includes the development of nano-sized particles and coatings for improved corrosion resistance, wear resistance, and enhanced surface properties.
- Sustainable Plating:The focus on sustainability is driving the development of environmentally friendly plating processes, using less hazardous chemicals, reducing waste generation, and promoting recycling and reuse of plating solutions.